Workforce Shortage Driving AI Adoption
Posted by PASI JULKUNEN
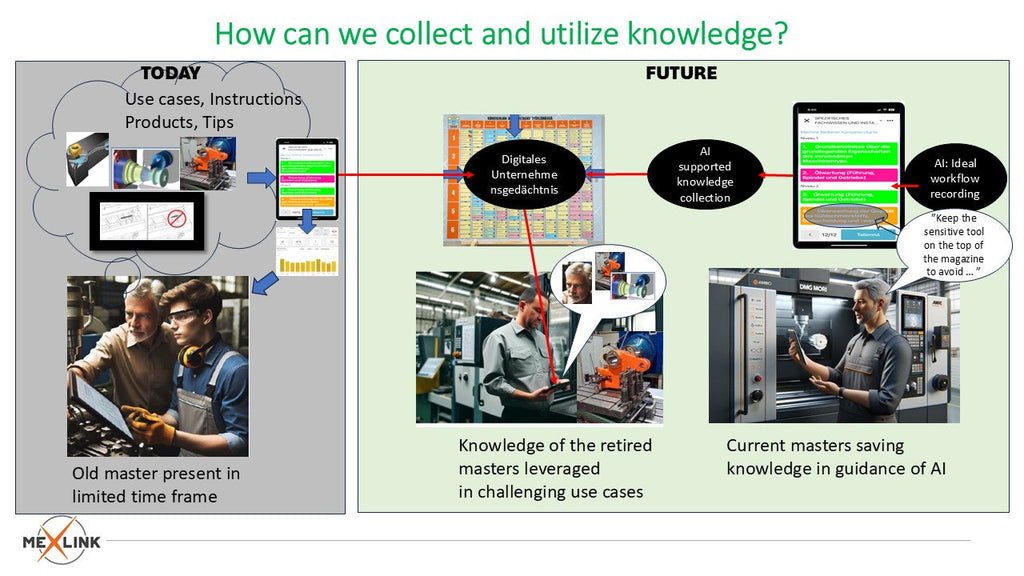
Repeating this inevitable, time-bound truth can feel frustrating when a solution exists, albeit with barriers still to overcome. Understanding how to wisely apply AI is increasing. In Germany, Sweden, Finland, and the Netherlands, nearly a quarter of manufacturing industry workers will reach retirement age within the next 5–10 years.
Companies face a dual challenge: retirement will remove a significant portion of experienced personnel, and new skilled workers are not being recruited fast enough. This directly threatens industry competitiveness and adaptability to ongoing major shifts such as energy and technological transitions.
MexLink’s advanced calculation model highlights the economic impact:
- The onboarding of new resources and their training requirements.
- The dilution of skills and its impact on the company's productivity potential.
In our example company, with a turnover of around €24 million, profitability is reduced by €2.6 million in turnover for the most difficult products to manufacture and EBIT falls by €2.3 million. Even for easy products, the figures are enough to raise the hairs on the back of your neck.
In our example company, shortening the onboarding time for new employees by a year corresponds to an additional €40,000 in revenue and an additional €27,000 in EBIT per onboarding of a new employee.
Figure 1. The impact of the distribution of skills on the profitability of a company (T1 beginner,.., T6 Master)
This situation causes a significant skills shortage, especially among practical professions such as machinists, maintenance technicians, and assemblers.
At the same time, new professionals are not enough to fill the gap. Vocational education and training and the transition to working life are currently not sufficiently attractive to young people. In Germany, thousands of entry-level positions in mechanical engineering remain unfilled, in Sweden only a fraction of students choose the industrial engineering program as their first choice, and in Finland and the Netherlands, the attractiveness of technical studies is still insufficient. In addition, outdated images and stigmas about jobs in the manufacturing industry have a negative impact on young people's attitudes.
Current challenges facing businesses and their causes
The problems are not only caused by the aging population, but also by companies' own decisions and strategic orientattions. Many companies postpone long-term human resource planning and talent strategies due to short-term financial challenges. Securing cash flow and immediate cost savings often take priority, increasing the risk of long-term skill shortages.
Moreover, the potential of automation and robotics has been overestimated. Nearly half of German SMEs believe robotics and automation can adequately replace retiring workers by 2032, despite reality showing this to be only partially achievable. Automation requires significant changes to factory machinery for efficient production flow, yet few companies can afford rapid investments in new production infrastructure. Sole reliance on automation is not a realistic solution, as much of the necessary skill is tacit knowledge, difficult for machines to replicate without the proper technological and organizational infrastructure.
Solution: AI Helps Preserve Tacit Knowledgehelps
Mexlink offers the solution with the artificial intelligence-based Mexwiser system. Mexwiser is designed to store and utilize the tacit knowledge that experienced employees have accumulated over the years. This "digital memory" allows valuable know-how to be preserved even when key employees leave the workforce. There is no other system on the market with such practicality, as it requires a unique combination of industrial experience and artificial intelligence technology.
On-the-job learning is the most important source of productivity for companies and is the subject of Mexwiser's digital corporate memory. Only 10% of learning comes from training, 20% from interacting with other people, and the remaining 70% through problem-solving on the job.
Figure 2. The importance of experiential learning
MexLink's approach
MexLink's approach emphasizes rapid impact, clear financial measurability, and the importance of investment. Mexwiser solutions are designed to meet EU AI regulatory requirements and provide immediate value to businesses alongside automation and robotics. This approach enables businesses to effectively respond to talent shortages and strengthen their ability to remain competitive and productive in the future.
The future belongs to the collaboration between artificial intelligence and humans
Although artificial intelligence and automation are key factors of the future, the combination of human expertise and machine intelligence is still crucial. Mexlink believes that the solution is not found in technology alone, but in how technology supports and complements human expertise. The cheap labor strategy has proven to be short-sighted, as Chinese industry, for example, is now realizing as it strives to shift to higher-quality production.
Mexwiser enables this synergy. It offers the manufacturing industry a way to secure expertise and competitiveness as generations change and new challenges raise increasingly demanding skill requirements.
Mexlink wants to be your partner in this transformation. Welcome to discuss with us how we can together ensure your company's competitiveness well into the future.
Figure 3. Mexwiser AI assistant as a company's digital memory